Over the centuries, great technical achievements led to the machines of today, which can grind solid particles at the rate of tens of thousands of tons per day. The evolution of machines from devices driven by one person to immense machines with capacities of many hundred tons per hour driven by motors larger than 20,000 kW (27,000 hp) has followed the path of technology in general, encapsulated by Henry Hodges (1970) in the final chapter of his book entitled Technology in the Ancient World:
Nowhere was the rate of technological advance a steady, even, upward climb.
Always one seems to be confronted with sudden bursts of technological innovation followed by long periods of virtual stagnation.
and
If the history of technology in the ancient world is to teach us anything at all it is to tell us that no technology can stand long on its own in glorious isolation. For a technology to thrive and develop required the presence of other often quite unrelated technologies alongside it from which ideas could be lent or borrowed. Such was the case, anyway, in the ancient world. One is left wondering whether the world of today is so very different.
TABLE 1.3 Energy consumed in grinding some widely used products
Material
|
Energy Used, kW-hr/t
|
Hard coal in power plants
|
7.6
|
Cement
|
67.5
|
Iron ore
|
40
|
Nonferrous ore
|
~30
|
Phosphate ore
|
~40
|
Inorganic pigment
|
880
|
Organic pigment
|
220
|
Wood pulp cellulose
|
1500
|
Cereals
|
26.5
|
Sugar, cacao, dried milk
|
45
|
Burnt lime
|
15
|
Source: Rumpf 1977.
|
THE CONTRIBUTION OF TECHNICAL AND NONTECHNICAL FACTORS
Key Technical Factors
■ Processes were developed late in the 19th and early in the 20th centuries for producing cement and metals. These techniques—the McArthur-Forrest process (invented by J. S. McArthur and R. and W. Forrest) for leaching fine-grained gold ores, the flotation process for concentrating sulfides in fine-grained metal ores, and the rotary kiln for making cement—required finer particles than the mills at the time could produce. The ball mills built for these processes eventually grew into the huge machines of the 21st century.
■ Electrical and mechanical engineering improvements allowed compact, high-power motors to be built and produce power to be transmitted efficiently into mill drives.
■ High-quality steels that were resistant to wear, impact, and fatigue were invented; these reduced equipment breakdowns and increased production rates.
■ Scientific advances led to better equipment and techniques for design and control.
Key Nontechnical Factors
■ When the economic regime that controlled taxation and the availability of capital and skilled labor was favorable, owners of plants in which grinding mills were used invested in new equipment, including new sources of energy and materials.
■ A vibrant mood of intellectual inquiry, which had been evident during the prosperous years of the Greek and Roman empires, the Renaissance, and the Science Age in the 19th century, emerged again during the second half of the 20th century, leading to much progress in size-reduction technology in Europe and the United States.
Karl Marx had no doubt about the importance of the grinding mill to the history of mechanical technology itself: “…the history of the development of machines may be retraced by the history of the flour mill” (Kuprits 1967).
As we review the history of size reduction, we should keep in mind that both technical and nontechnical factors came into play in the technology’s evolution, particularly in the 20th century (see sidebar). In the rest of this chapter we review how sources of energy, quality of materials, and investments in technology changed the practice of size reduction (see Table 1.4 and Figure 1.2).
8 | THE HISTORY OF GRINDING
|
|
TABLE 1.4 The progress of size-reduction technology*
|
|
Stages in Technology Development
|
Factors Interacting at Each Stage
|
Human muscles
Men or animals working together
Waterpower
Steam power
Electricity
|
Available materials Accumulated skills and experience Economic and social conditions Religious and ethical tenets Philosophical doctrines
|
Energy Available per Machine
|
Power Delivered by Muscles, ft-lb/sec
|
Stone Age—Human muscles: 0.1 kWt/person 600 BC—Men or animals working together: 0.5 kW 100 BC—Water wheel: 5 kW*
1800—Steam engine: up to 50 kW§
1900—Electricity: 30,000+ kW (no limit)
|
Draft horse: 432 Ox: 288 Mule: 216 Donkey: 108 Human pumping: 33 Human winching: 45
|
Source: Adapted from Forbes 1955.
|
* We do not include explosive energy in the table because its growth has been separate from the growth of mechanical size reduction; however, explosives have been crucially important in size reduction, and the same interacting factors apply.
t 1 hp (0.746 kW) = 500 ft-lb/sec.
* Large water wheels generated more than 50 kW, but 5 kW seems a reasonable estimate for power used by many grinding machines operated by waterpower.
§ 50 kW is a reasonable estimate for steam engines used to drive grinding machines.
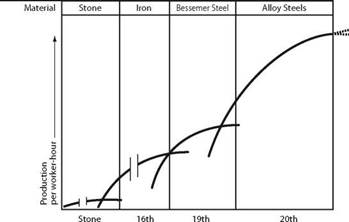
Table 1.5 gives a brief chronology of size-reduction technology, and Table 1.6 presents a more detailed chronology. (Italics denote an event that contributed to substantial progress in size-reduction technology.)
TABLE 1.5 Brief chronology of the development of energy used for size-reduction technologies
Time Frame
|
Technology
|
Effects
|
Muscle Power
|
Stone Age
|
Mortars and pestles
|
Pounding action; good for coarse grinding
|
2000 BC
|
Saddlestones
|
Reciprocating action; good for fine grinding
|
500 BC
|
Querns
|
Rotary action; good for grinding soft grains, less satisfactory for grinding hard ores
|
Waterpower
|
1500 AD
|
Stamp mills driven by water wheels
|
Pounding action; good coarse-grinding machine
|
Steam Power
|
1850-1900
|
Jaw crushers, ball mills, air classifiers
|
High-capacity machines for ores and cement
|
|
Roller mills for grains
|
Precise machines to grind grains incrementally
|
Electricity
|
1900-1920
|
Vertical roller mills, rake classifiers,
|
Closed grinding circuits for ores, coal, and
|
|
autogenous pebble mills
|
cement; stones used as grinding media
|
1930-1955
|
Primary autogenous mills
|
Rocks or ore used as grinding media
|
1960-1975
|
High-diameter, short-length
|
Eliminated crushers in iron and copper ore
|
|
semiautogenous mills
|
circuits
|
1985-1999
|
Large tumbling mills, high-speed stirred mills
|
Very high-capacity and very fine-grinding machines
|
|
TABLE 1.6 Full chronology of size-reduction technology
Source of Power
|
Time Frame*
|
Machines and Processes
|
Muscle Power
|
People
|
Stone Age
|
Mortars and pestles; hand stones; rock masses broken by fire and stone hammers
|
|
2500 BC
|
Hand-operated bellows for compressed air
|
|
2000 BC
|
Saddlestone mills
|
|
1500 BC
|
Foot-operated bellows for compressed air
|
|
500 BC
|
Rotary querns
|
Cattle
|
200 BC
|
Rotary querns
|
Water Wheels and Windmills
|
Horizontal wheel
|
100 BC
|
Water-driven rotary querns, initially in east Mediterranean
|
Vertical wheel
|
20 AD
|
Water-driven rotary querns, initially in Roman Empire
|
Windmill
|
700
|
Wind-driven rotary querns, initially in Persia, Afghanistan
|
|
200
|
Edge roller mills in China for fine grinding
|
Vertical water wheel
|
400
|
Waterpower replaced muscle power for grain milling in Roman Empire
|
|
800
|
Dry stamp mills (manual power)
|
|
1320
|
Black powder used for military purposes
|
|
1512
|
Water-driven wet stamp mills
|
|
1546
|
De Re Metallica: Agricola’s textbook on mining engineering
|
|
TABLE 1.6 Full chronology of size-reduction technology (continued)
Source of Power Time Frame*
|
Machines and Processes
|
1558
1587
1589
1627
1776
1785
|
Corrugated roller mill for grains—not used for 300 years Amalgamation process for silver extraction Arrastra for grinding and mixing in amalgamation process Black powder used for mining purposes Mechanical air compressor Oliver Evans’ automatic flour mill Steam
|
Steam engines 1800 1827 1831
|
Cornish roll crushers invented to grind ores in Cornwall, England Portland cement produced
Bickford miners’ safety fuse invented for blasting with black powder in Cornwall
|
1838
1839
1840
1847
1848
1849
1847 1858 1860 1867 1867 1867 1870
1870
1870 1876 1880
|
Singer steam churn drill
Iron roller mills for grinding grains
Patent for hammer mill
Nitroglycerin introduced as first high-energy explosive William Easby’s high-pressure, double-roll compactor Mechanical percussion drill
Fine sieves and aspirators for flour sifting and purification
Eli Blake jaw crusher
Rock drill powered by compressed air
Dynamite made from nitroglycerin
Fulminate of mercury blasting cap invented for nitroglycerin Peter von Rittinger’s energy-size reduction theory (first theory) Rotary kiln to produce cement clinker Alsing batch ball mill for grinding flint for potteries Tripod-mounted rock drills
Gebruder Sachsenberg’s screen-discharge ball mill Corrugated iron rolls used for grain milling, leading to gradual reduction system
|
1881
1885
1885
1888
1889
1891
1895
1895
1895
1898
1898
|
Philetus Gates’ gyratory crusher Askham dry air separator
Friedrich Kick’s energy-size reduction theory (second theory) Vertical roller mill (F. E. Huntington’s mill)
Cyanide process for gold extraction First patent on hydrocyclones
Electric delay blasting caps invented by H. Julius Smith Thomas Edison’s giant rolls Water-flushed hammer drills
Ball mills used to grind gold ores in South Africa, Australia Medium-speed pin mill Electricity
|
Electrical motors 1900
1904
1905
1906
1904 1909
|
Vertical ring-roller and ring-ball mills for coal and soft ores J. V.N. Dorr’s mechanical hydraulic classifier Flotation process for sulfide ores Harlowe Hardinge’s conical mill
Pebble milling used on the Witwatersrand (the Rand), South Africa Cryogenic breakage
|
|
TABLE 1.6 Full chronology of size-reduction technology (continued)
Source of Power Time Frame*
|
Machines and Processes
|
1910
|
Rod mills
|
1910
|
Raymond ring-roller mill (fixed ring)
|
1920
|
Multiple-compartment tube mills
|
1928
|
Loesche GmbH’s roller mill (rotating bowl)
|
1928
|
Vertical stirred ball mill
|
1930
|
Will Symons’ cone crusher
|
1930
|
Vibrating ball mill
|
1932
|
Alvah Hadsel’s wet primary autogenous mills
|
1933
|
Rosin-Rammler equation to define size distributions
|
1935
|
Tromp size separation curves
|
1941
|
Hardinge’s "electric ear” for feed control
|
1942
|
Dutch State Mines’ cyclone for coal circuits
|
1944
|
Humphrey Investment Company’s cyclone with vortex finder
|
1948
|
Hydrocyclones for ore circuits
|
1950
|
Tungsten carbide drill bits
|
1950
|
Jet mill
|
1951
|
Fred Bond’s energy-size reduction theory (Third Theory)
|
1952
|
Delay detonators
|
1955
|
Kubota Company’s tower ball mill
|
1956
|
Kelly Krebs’ hydrocyclones
|
1956
|
Broadbent-Callcott breakage-selection-classification matrix model for grinding mills
|
1957
|
Ammonium nitrate slurry explosives
|
1958
|
Jack Williamson’s load-power-feed rate controller for pebble mills
|
1960
|
Second-generation air separators with external cyclones
|
1960
|
Down-hole hammer drills
|
1963
|
Vertical high-speed "John” peg mill 205
|
1970
|
Vertical-shaft impact crushers
|
1975
|
Centrifugal mills
|
1975
|
Computer-control techniques for grinding circuits
|
1976
|
Nonelectric delay caps
|
1977
|
High-pressure grinding rolls
|
1980
|
Third-generation high-efficiency air separators
|
1980
|
Computer-simulation techniques for mineral grinding circuits
|
1993
|
High-speed horizontal disk mill
|
1995
|
Very large roller and tumbling mills for minerals (~1,000 tph)
|
* Most dates are indicative.
|